The Intelligent Operation Center (IOC) is a vital place that monitors, tracks and operates daily activities, especially in the fields of production and business. Currently, many power generation companies own various hydroelectric plants, wind power clusters, and solar power plants. The production clusters are located in different geographical areas, across many provinces and cities. Each production cluster requires a number of dozens of people on duty (depending on the size of the plant). It costs a lot to maintain a duty team. In addition, it also poses challenges for the supervision and management of the board of directors.
With the support from the IOC, the process of digital transformation becomes more convenient, reducing the burden on leaders, management and operation agencies.
Functions of IOC
The OCC center is a centralized system that integrates all the monitoring and control functions of various power generation clusters. It is connected to an operating room near the executive board of the company, where the operator can manage the machine operations, electrical parameters and incidents remotely. The OCC center also has camera and phone systems that allow the management board to supervise the production clusters and communicate with the field operations.
Some benefits of having an OCC center are:
– Lower operating costs for on-site staff. Only 1-2 staff members are needed per shift to monitor all the activities of the power production clusters. A small team is maintained on-site for emergency situations.
– Better production visibility for the management board.
– Faster data and incident reporting from a single source.
– Improved management efficiency and productivity.
– Reduced travel time and expenses for the leadership and management, who can monitor the production clusters from a distance.
The role of IOC
IOC has four main functions:
– Planning center: It uses big data technology to analyze and use information, to find the key points and challenges in management and operations, and to support decision making.
– Warning center: It predicts possible risks and gives early warnings, to make sure there are plans to prevent and deal with emergencies.
– Administration center: It collects, processes and monitors comprehensive data through infrastructure such as computer vision, cameras, sensors or industrial switches. It improves collaboration efficiency, quick response, resource optimization and factory management.
– Emergency command center: It coordinates multiple departments, divisions and forces to assign actions and resources when an emergency happens. It supports communication, video, visual consultation and office operation on any device, across levels, regions and departments. It ensures the command center is always accessible no matter where the operator is. This helps officials make fast and informed decisions remotely.
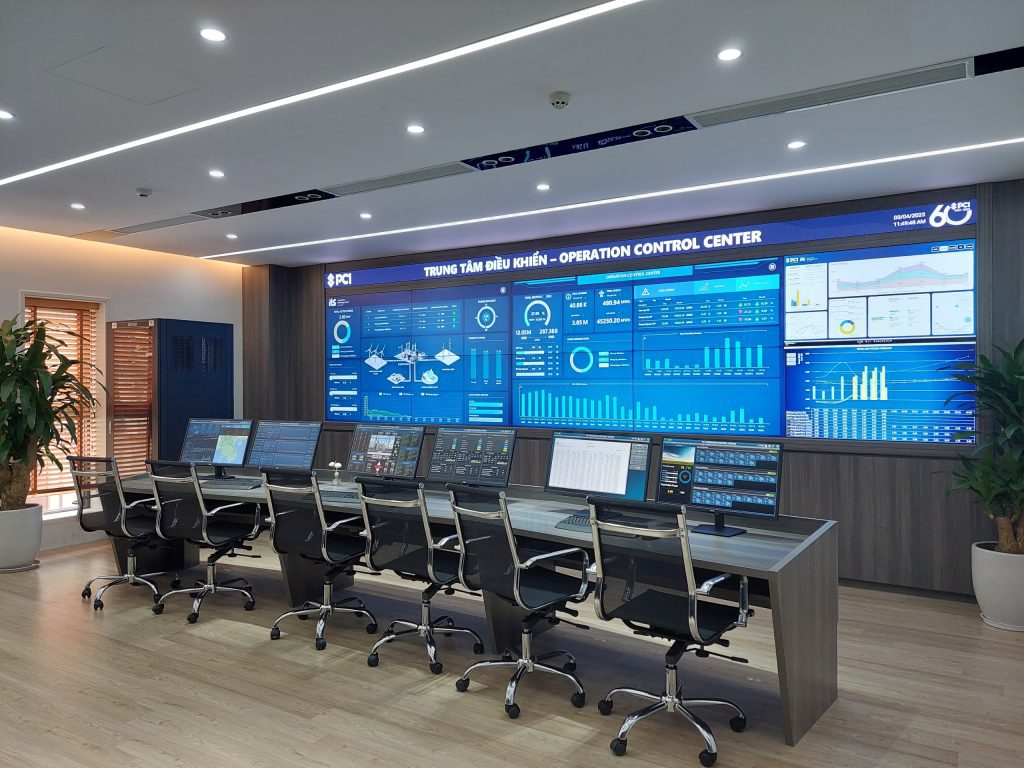
Implementation plan
The central operating room is the heart of the operating board, where the operator can remotely monitor and control the plants. It has a spacious and modern design, with tables and chairs, computers, network equipment, and electrical cabinets. The most striking feature is the large LED screen on the wall, which shows various control and monitoring interfaces for the plants. The operator can switch between different views, such as the generator set control and the water level camera on the channel. The room provides a flexible and efficient operating space for the operator.
The IOC system uses secured network system to connect various signals from the plant to the control room. These signals include control, electrical, water level, and mechanical parameters, as well as plant incidents and machine status. The signal retrieval does not interfere with the existing SCADA/DCS system, and the plant can operate normally during the installation.
The user interface is designed to be simple and intuitive, with no redundant signals on the same screen. The system also provides tools to measure the operation time of each unit, and to classify and count the electrical and mechanical incidents. These features help the management to plan the equipment maintenance more efficiently.
The system also supports database creation based on production hours and dates. The electricity output for different time periods is displayed on charts. This helps the management to monitor the production performance of the plant without relying on daily reports.